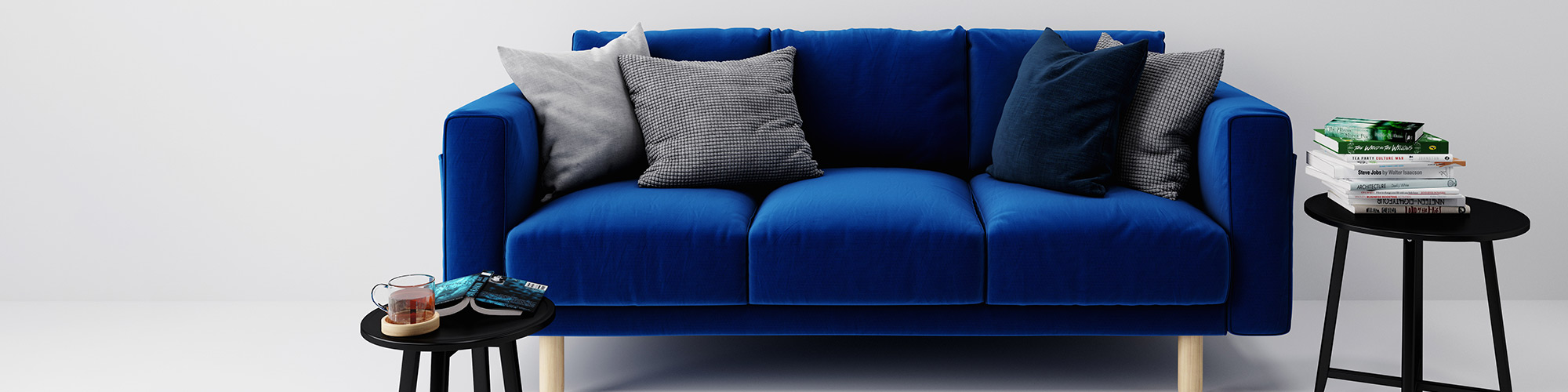
Royal Solid Rigid Core Resources
We try to provide our customers with the most useful tools at our disposal. Quickly locate frequently asked questions, installation guide, downloads, environmental and performance data in the tabs below.
Downloads
We try to provide our customers with the most useful tools at our disposal. Quickly locate and download product data, technical specifications, installation guides and other documents below (all open as an Adobe© PDF or ZIP).
Brochures
Installation
Environmental
ACP, the parent company of Lico, believes in the importance of sustainability. We are committed to not harming the environment or depleting natural resources to make our products.
Environmental Policy
As a responsible corporate citizen, ACP is dedicated to protecting human health, natural resources, and the global environment. This commitment extends beyond compliance with the law to encompass integration of sound environmental practices into our business decisions.
Manufacturing
Our manufacturing facilities continuously pursue methods to further reduce operating emissions, recycle all waste material, and use the safest raw materials with the least environmental impact.
Personnel
Every employee receives sustainability training pertinent to his/her job responsibility. All plastic, paper, aluminum and wood is recycled in every department.
Sustainability accomplishments
- Building reuse
- Manufacturing waste management – 99% of manufacturing waste is recycled
- Recycled content – up to 60% depending on product
- Regional materials
- Some rapidly renewable materials
- Low-emitting adhesives and sealants
- Low-emitting, water-based paints, coatings and inks.
- Low-emitting materials
Environmental Philosophy
We recognize that preserving natural resources by minimizing adverse environmental impact is vital, and we are committed to providing all of our customers with high-quality, environmentally-friendly products. We have a longstanding commitment to conserving natural resources and protecting the health and well-being of our customers by:
- Reusing and recycling materials and creating products that are recyclable.
- Developing products that are safe for their intended use and will not adversely affect indoor air quality.
- Striving continuously to create new green products and make current products more environmentally efficient.
- Keeping customers informed of the full environmental benefits of products and how to incorporate them into new projects for potential LEED Credits.
Indoor Air Quality
We are dedicated to indoor air quality. Over the last several years, much attention has been focused on air pollution. Until recently, few scientists paid much attention to the quality of air within homes and other buildings, despite the fact that U.S. government research indicates that people spend approximately 90% of their time indoors. In many cases, the air within buildings can actually be more polluted than the air outside. Given the amount of time most people spend inside, the potential exists for a health-related disaster.
Performance
Fire Rating
All Lico flooring products have a ‘Class A’ FSI and SDI fire rating per ASTM E84. Our flooring products are rated for surface burning characteristics, flame spread and smoke development.
Significance and Use
- 4.1 This test method is intended to provide only comparative measurements of surface flame spread and smoke density measurements with that of select grade red oak and fiber-cement board surfaces under the specific fire exposure conditions described herein.
- 4.2 This test method exposes a nominal 24-ft (7.32-m) long by 20-in. (508-mm) wide specimen to a controlled air flow and flaming fire exposure adjusted to spread the flame along the entire length of the select grade red oak specimen in 51/2 min.
- 4.3 This test method does not provide for the following:
- 4.3.1 Measurement of heat transmission through the tested surface.
- 4.3.2 The effect of aggravated flame spread behavior of an assembly resulting from the proximity of combustible floors.
- 4.3.3 Classifying or defining a material as noncombustible, by means of a flame spread index by itself.
1. Scope
- 1.1 This fire-test–response standard for the comparative surface burning behavior of building materials is applicable to exposed surfaces such as floors. The test is conducted with the specimen in the ceiling position with the surface to be evaluated exposed face down to the ignition source. The material, product, or assembly shall be capable of being mounted in the test position during the test. Thus, the specimen shall either be self-supporting by its own structural quality, held in place by added supports along the test surface, or secured from the back side.
- 1.2 The purpose of this test method is to determine the relative burning behavior of the material by observing the flame spread along the specimen. Flame spread and smoke developed index are reported. However, there is not necessarily a relationship between these two measurements.
- 1.3 The use of supporting materials on the underside of the test specimen has the ability to lower the flame spread index from those which might be obtained if the specimen could be tested without such support. These test results do not necessarily relate to indices obtained by testing materials without such support.
- 1.4 Testing of materials that melt, drip, or delaminate to such a degree that the continuity of the flame front is destroyed, results in low flame spread indices that do not relate directly to indices obtained by testing materials that remain in place.
- 1.5 The values stated in inch-pound units are to be regarded as standard. The values given in parentheses are mathematical conversions to SI units that are provided for information only and are not considered standard.
- 1.6 The text of this standard references notes and footnotes that provide explanatory information. These notes and footnotes, excluding those in tables and figures, shall not be considered as requirements of the standard.
- 1.7 This standard is used to measure and describe the response of materials, products, or assemblies to heat and flame under controlled conditions, but does not by itself incorporate all factors required for fire-hazard or fire-risk assessment of the materials, products, or assemblies under actual fire conditions.
- 1.8 This standard does not purport to address all of the safety concerns, if any, associated with its use. It is the responsibility of the user of this standard to establish appropriate safety and health practices and determine the applicability of regulatory limitations prior to use.
- 1.9 Fire testing is inherently hazardous. Adequate safeguards for personnel and property shall be employed in conducting these tests.
Moisture
Lico flooring products are waterproof. Our flooring products are guaranteed not to water-stain, bow, swell or rot. They are ideal for use in moist and humid environments like basements.
Mold & Mildew Resistant
Lico flooring products are constructed from materials that inhibit mold and mildew. This means our flooring products can be installed in a variety of environments where moisture is a concern dlouhygaragedoorrepair.com. They are manufactured from rigid core board and PVC or mineral core with a smooth or decorative, embossed surface texture. These waterproof floors solve the problems of water damage and mold or mildew that are traditionally experienced with many laminate flooring products.
- No water stains, no moisture-related sagging, no rot
- Mold and mildew resistant
- Nonporous, nonabsorbent
- Hygienic, easy to clean, easy to disinfect
Food Safety – FDA and USDA Compliant
Our Lico flooring products comply with FDA and USDA regulations for use in food preparation and serving areas. This means that our flooring can be installed in areas where sanitation and cleanliness is a must. Lico flooring products are fully compliant with the USDA, State health departments, and FDA requirements. Lico flooring products are also compliant with the Canadian Food Inspection Agency.
FDA Food Code: Chapter 6 – Physical Facilities
Indoor Areas
6-101.11 Surface Characteristics
- Except as specified in (B.) of this section, materials for indoor floor surfaces under conditions of normal use shall be:
- SMOOTH, durable, and EASILY CLEANABLE for areas where FOOD ESTABLISHMENT operations are conducted;
- Closely woven and EASILY CLEANABLE carpet for carpeted areas; and
- Nonabsorbent for areas subject to moisture such as FOOD preparation areas, walk-in refrigerators, WAREWASHING areas, toilet rooms, mobile FOOD ESTABLISHMENT SERVICING AREAS, and areas subject to flushing or spray cleaning methods.
- In a TEMPORARY FOOD ESTABLISHMENT:
- floors may be constructed of a material that protects the interior from the weather and wind-blown dust and debris.
Cleanability
6-201.11 floors
- Except as specified under § 6-201.14 floors and floor coverings shall be designed, constructed, and installed so they are SMOOTH and EASILY CLEANABLE.
6-201.12 floors and Utility Lines
- Utility service lines and pipes may not be unnecessarily exposed.
- Exposed utility service lines and pipes shall be installed so they do not obstruct or prevent cleaning of the floors.
- Exposed horizontal utility service lines and pipes may not be installed on the floor.
USDA Electronic Code of Federal Regulations: Title 21 – Food and Drugs
§ 110.20 Plant and Grounds
- Plant construction and design. Plant buildings and structures shall be suitable in size, construction, and design to facilitate maintenance and sanitary operations for food-manufacturing purposes. The plant and facilities shall:
- Be constructed in such a manner that floors may be adequately cleaned and kept clean and kept in good repair; that drip or condensate from fixtures, ducts and pipes does not contaminate food, food-contact surfaces, or food-packaging materials; and that aisles or working spaces are provided between equipment and floors and are adequately unobstructed and of adequate width to permit employees to perform their duties and to protect against contaminating food or food-contact surfaces with clothing or personal contact.
- Provide adequate lighting in hand-washing areas, dressing and locker rooms, and toilet rooms and in all areas where food is examined, processed, or stored and where equipment or utensils are cleaned; and provide safety-type light bulbs, fixtures, skylights, or other glass suspended over exposed food in any step of preparation or otherwise protect against food contamination in case of glass breakage.